Loom - modernization
- Home
- Machines and devices
- Krosno – modernizacja
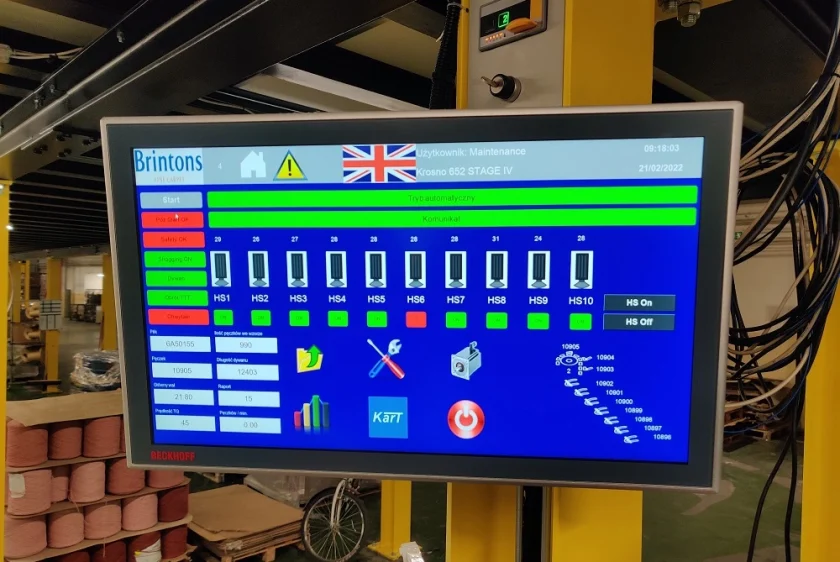
The completed modernizations enabled the loom to produce products with 32 different yarn colors (previously, it was only possible to produce carpets with a maximum of 16-20 yarn colors). With 32 colors, the loom operates at a speed of approximately 15 bundles per minute.
The Tuft Generator has been equipped with an innovative EOD (electronic optical device) board. The previous board had two sensors (a base sensor and an analog sensor for yarn detection). The signal cable was connected to a connector, which, due to vibrations during normal operation, would slip out, causing the loom to stop. In the new EOD board, there is one sensor – the base sensor is eliminated, and the analog sensor has been replaced with a digital sensor (0 or 1 signal). The board is equipped with a new connector for connecting the signal cable. The signal cable is mounted on an M8 connector (3-pin). In this version, during operation, the connector with the cable does not slip out from the EOD board. Additionally, the board is now equipped with an innovative yarn detection sensor cleaning system, which uses compressed air to blow on the optical sensor, preventing sensor contamination during normal operation.
A new system (Pilz 402240 PIT m3.3p) has been installed to manage authorization levels during loom operation. Coded keys with appropriate access levels for operators and service personnel have been implemented, allowing certain functions to be unlocked. The service mode operation does not require logging in or entering a password.
We removed the inductive sensors for basing and the limit sensors for movement at the extreme positions: left and right, from the loom. Using TwinCat 3 software, we implemented the memory of the base position for the Traverse axis in the servo encoder (the position is saved even after power is turned off). In the program, the Right Limit and Left Limit were set as positions (software limits). This allowed us to reduce wiring and components that could potentially be damaged.
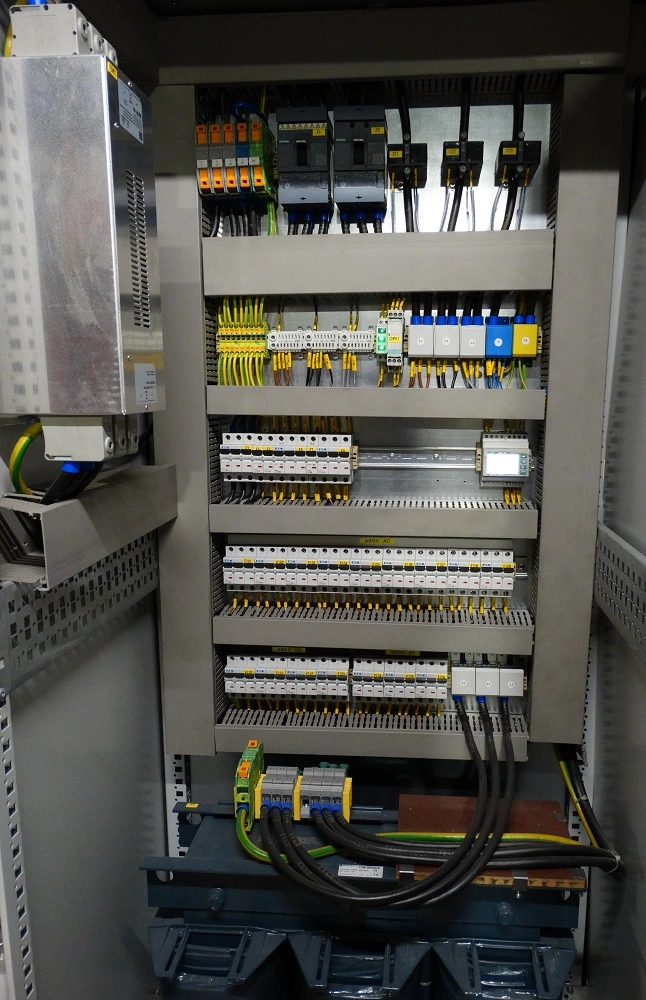
We removed the base sensor for the TG axis (the drive shaft for the Tuft Generators) from the loom. Using TwinCat 3 software, we implemented the memory of the base position for the TG axis in the servo encoder (the position is retained even after power is turned off). The programmed movements for the TG axis are modulo 360 degrees.
We installed a new inductive sensor on the TG shaft that detects the angular displacement of the TG motor and the TG shaft on the dog clutch during operation.
For the first time, we introduced a special Cam In/Out function in the program to couple the main axis (master/TG) with the subordinate axes (slave/HS1 to HS10 (Head Selector)). The Cam In/Out function enabled the movement of the HS1 to HS10 axes only when the TG shaft was correctly aligned at the required angle. The TG axis was programmed as the master relative to the HS1 to HS10 axes. Synchronizing the movements of these axes allowed the loom to operate at varying speeds ranging from 1% to 100%. Operating the loom at 1% speed enables quick diagnostics during loom repairs. The implemented Cam In/Out function has not been used in any machines of this type before. The use of this function was made possible by the new TwinCat 3 software.
We implemented the STO (Safety Torque Off) safety function for all drives in the loom when the emergency stop button is pressed, and for all drives except HS1 to HS10 when the front cover is opened. The function is implemented using TwinCat 3 software over the Safety over EtherCat network.
We implemented the SLS (Safety Limited Speed) safety function for the HS1 to HS10 drives in the loom when the front cover is opened. The function is implemented using TwinCat 3 software over the Safety over EtherCat network. When the front cover is opened, the HS1 to HS10 servos can move at a reduced speed, allowing the selector to be set in the starting position. After the selector is positioned in the starting position, we can store this position in the encoder memory of the HS1 to HS10 servos.
We installed a new bolt (Pilz 570400 PSEN ml b 1.1 unit) on the main cover to enhance operator safety during cover opening. The bolt is redundant with a coded key for SIL3/PL e/Cat4.
We installed a new brake on the main shaft of the Stage IV loom. We implemented simultaneous braking of the loom using both the brake on the main shaft and the slack adjuster on the main motor.
During carpet repair after the loom has stopped, there is the possibility for "additional" repair of specific areas with an accuracy of up to one bundle, within a range of 1 to 1104 bundles. On all older looms, it is only possible to repair areas where the sensor detected a missing bundle or to repair an entire section handled by a single Tuft Generator.
We introduced a new function called "Fill Report" (for bundle rows from 1 to 1104). Pressing the button on the HMI panel causes only a single report to be filled, after which the loom transitions to Stop mode.