Pet Food production line
- Home
- Production lines
- Pet Food production line
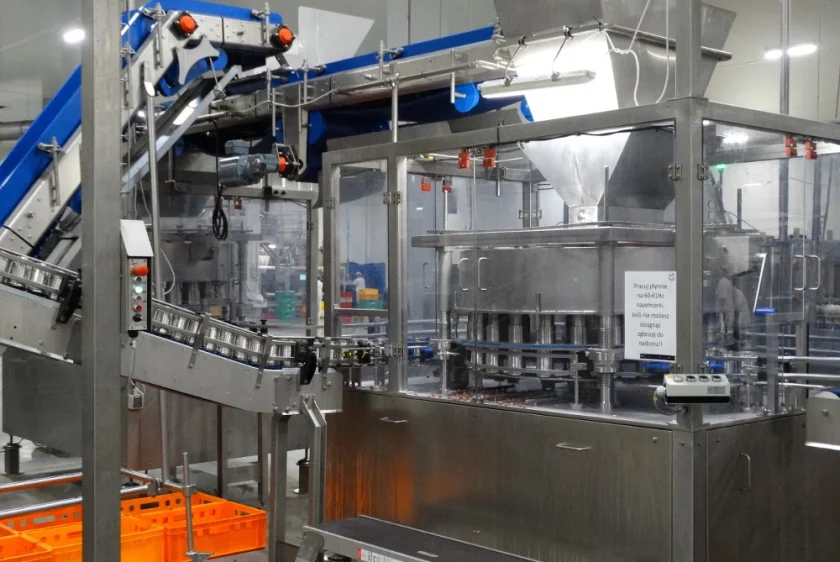
All devices are built as frame structures made of closed profiles and are entirely made of acid-resistant steel.
The first stage is delivering the meat paste to the stuffing pump. This is usually done using trolleys, with the food being fed into the funnel of the pump using a tipping device, which lifts and flips the trolley upside down—allowing for the gravitational dosing of the meat paste.
Next, the device pumps the paste through a pressure hose into a die, extruding strips of meat onto the belt of the steam tunnel. The meat strips are introduced onto the belt into the cooking chamber, where they undergo heat treatment using steam. The travel time through the steam tunnel is adjustable and depends on the die used, and thus on the thickness of the meat strips.
The next device in the line is the cooling tunnel, where the cooked meat is introduced and subjected to a cooling process using an air cooler. Additionally, the device is equipped with a water cooling system. After cooling, the cooked meat strips achieve the appropriate firmness, allowing them to be cut into pieces without tearing the meat structure – this process is carried out at the exit of the cooling tunnel by the cutting system.
The meat chunks, cut into pieces, fall onto a Z-type conveyor, which carries the food to the hopper of the can filler. The filler is loaded from the top, and the food is dosed volumetrically into the cans. The cans to be filled are delivered by a plate conveyor (they are placed manually on a rotary table and buffered on the conveyor). The cans filled with food are then transported on a conveyor to the can seamer, where they are filled with sauce
The final step is sealing the cans in the seamer. The filled and sealed cans are then transferred to the next stages of production in the plant.